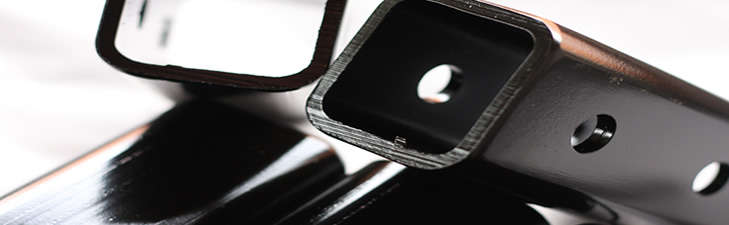
![]() |
What are some important design considerations for E-coat? |
When designing parts for Ecoat it is important to remember that the parts must be processed through multiple stages of various solutions.
It is critical that parts designed for Ecoat systems, submerge easily, drain freely and quickly and don't carryover solutions into subsequent stages. Likewise parts which entrap air during processing can cause areas of non contact resulting in uncoated areas in the finished product.
Consultation at the design stage will ensure correct placement and quantity of holes or notches for air release and drainage.
Product presentation in relation to metal substrate quality and cleanliness is paramount for e-coat systems as there are only light cleaning stages within the system. Only approved water soluble oils can be processed so consultation in this area is extremely important.
Solving part design issues prior to arrival for processing prevents costly manufacturing and processing delays.
read more about the Ecoat process

![]() |
Finishes "...Learn more about our durable range of Automotive and Industrial finishes" | ![]() ![]() ![]() |